Impregnated
CHARACTERISTICS OF IMPREGNATED TOOLS
They are tools whose cutting action occurs by abrasion. The cutting part is made of synthetic diamond powder contained in a mixture of tugsteno powders and copper-based alloys which, through an infiltration process in the furnace, melt and bind the various components forming what is called the tool matrix. The matrix is the cutting part of the tool.
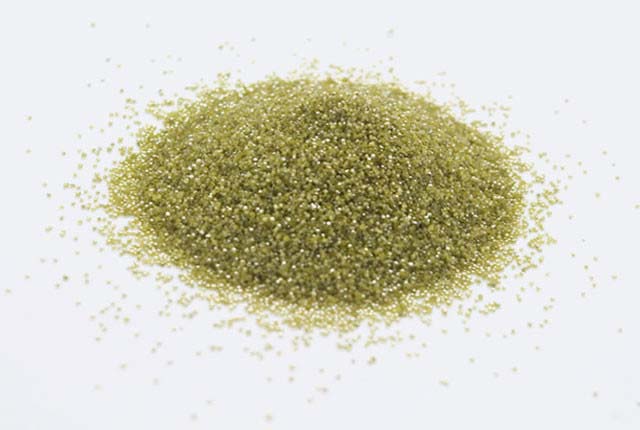
During the drilling time, which occurs by abrasion, the cutting edge of each single exposed diamond as well as the concretion that holds it in the matrix tends to wear out. The wear out of the concretion will cause the detachment and the consequent loss of worn diamonds exposing new ones (placed below to those worn) with intact cutting edge and suitable for cutting. The materials to be drilled have very different characteristics of resistance to abrasion and hardness and for this reason it is necessary to treat them with tools having appropriate matrices.
Varying the size and quantity of synthetic diamond powder, as well the size and density of tungsten powders, using different types of binder, NEXUS has drafted multiple series of matrices with different hardness and abrasion resistance, in order to adapt them to the multiple characteristics of the materials to be drilled . In order to reduce the using costs of the tool as much as possible, in general, very hard materials will be tackled with tools having soft and vice versa matrices; very abrasive materials will be processed with tools having abrasion resistant matrices and vice versa. This technology is applicable for drilling materials with variable hardness from 80 to 500 MPa.
NEXUS has implemented a series of matrices that are identified with a letter that identifies the impregnated product line (eg O=ORION; C=CAPRICORN; A=AIRES; X=TAURUS) and by a number that identifies a reduction of hardness from the matrix and consequently the possibility of being used on harder materials. Unfortunately it is not enough to identify the type of rock to be drilled to identify the suitable matrix, since in the performing of a hole there are other variables that have a decisive influence on the effectiveness of the cutting.
The depth and the direction of the drilling, the level of fracturing of the rock, the variability of materials within the same hole, the characteristics of the probe (number of revolutions, torque, thrust on the tool) have a decisive influence on the choice of the matrix most suitable and therefore these data must be evaluated carefully before making a choice. In addition to the standard range of matrices, NEXUS is able to draft special matrices optimized for a specific uses. These tools have to be used using water as a drilling fluid for tool cooling and debris removal.